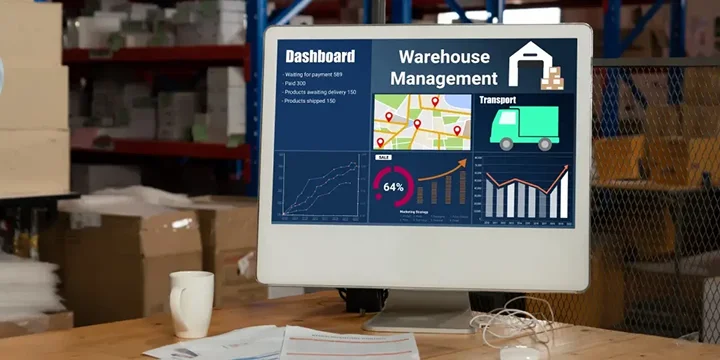
Table of Contents
About Our Client
The client is a mid-sized business based in the United States of America that is a cold storage company that is FDA-certified and licensed for third-party cold storage for other businesses storing perishable commodities. They dealt with vast stocks of sensitive goods and had problems with warehouse and dispatch management of stocks and inventory, especially as… Due to this, they needed a sound system to be able to meet the customer’s needs as well as provide efficient mechanical handling in a warehouse and dispatch.
Problems
The client was having some challenges operating their cold storage and dispatch before introducing the warehouse management system. Temperature-sensitive products had to be controlled for inventory, and this was not achievable when using manual systems. Regular shortages of stock, specifically with products that are perishable, caused product loss as well as customer complaints.
However, it forced main functions to be poorly coordinated in dispatch operation, with consequences of the delay of shipments, confusion, and problems with delivery timetables. Due to the noticeable lack of real-time transparency of the client’s warehouses and overall logistics, the expected optimization of storage space and improvement in dispatch failed to unravel; operational costs went up, labor turnover became a huge problem, and there were lost prospects for business advancement.
Solutions
Based on the client’s requirement, Celestial Infosoft designed a warehouse management system with a dispatch management system solution. Key solutions provided include:
- Automated Inventory Management: Inventory control is provided through the current status information of items in each location and helps the business avoid situations where perishable stocks go bad.
- Temperature Monitoring and Alerts: The system also follows the temperature of stored items to check conformity to standards and will send notifications in case of a variation.
- Dispatch Management Integration: Our solution enhances the synchronization of the warehouse and the dispatch; it provides a platform for the automatic processing of orders; it also provides optimal routes to follow when delivering; as well as the tracking of the vehicles in delivery for efficient delivery.
- Order Fulfillment Automation: The WMS also supports order picking, packing, and shipping to expedite accurate order delivery to the client’s customer.
- Real-Time Visibility and Reporting: Real-time tracking of both the current stock position of the warehouse in addition to the schedule for dispatch of the inventory is made available through a centralized dashboard, allowing the client to effectively manage the cold storage solutions as well as the related logistics.
Results
The client has gained improved efficiency, especially after the beginning of using the integrated warehouse and dispatch management system. As of now, they control their stocks and avoid overstocking by using updated records; perishable products are well managed for storage and transportation. One of the major impacts of automating order fulfillment and dispatch management has been the elimination of many months of shipment delay for improved delivery of goods and an upgrade of customer satisfaction.
Furthermore, through real-time tracking of the system, the client has been able to monitor space and logistics and gains a 40% operating advantage in addition to cutting down on operational costs greatly. The client can now engage in business development since they know that their demand will increase and they will serve it efficiently and effectively.
Connect With Us You Won’t Regret
Our team is ready to provide you with client references, give you an individual quote for your project, or advise on any question contributing to your IT project.
More Case Studies
-
Powering the UK’s Smartest Beauty & Wellness Booking MVP
Discover how Celestial Infosoft built Spare Chair, a UK-based MVP connecting users with beauty and wellness professionals. Read more
-
Scalable Payment Gateway Integration for a Digital-Only Bank
IndustryBanking & Fintech TechnologiesJava, PostgreSQL, AWS About Our Client Our client is a digital-only bank based in Southeast… Read more
-
Web and Mobile Banking Software for Seamless Digital Banking Experience
IndustryBanking & Financial Services TechnologiesFlutter, .NET Core, Firebase About Our Client Our client is a mid-sized cooperative bank… Read more
-
Custom Customer Portal for Seamless Digital Banking
IndustryBanking & Financial Services TechnologiesReact.js, .NET Core, Azure SQL About Our Client The client is a mid-sized commercial… Read more